Raw Matarrial
Direct Reduced Iron
A Revolution in the Steel Industry
Introduction to Direct Reduced Iron
Direct Reduced Iron is a valuable product in the steel industry that is produced through the direct reduction of iron ore. In this process, without the need for melting iron ore, its oxygen is removed, and a porous pellet with 67% iron content is produced. This product, after melting and casting processes, is transformed into various forms such as slabs, billets, and re bars.
Reasons for Using Direct Reduced Iron
Direct Reduced Iron is named after its spongy structure. This product serves as an excellent alternative to scrap iron and offers numerous advantages:
High Iron Content: It has a high percentage of pure iron.
Reduced Dependence on Scrap Iron: By reducing the need for scrap iron, it helps stabilize the steel market.
Eco-Friendly: It has lower environmental impacts due to reduced pollutants and waste.
Improved Production Efficiency: Due to its higher quality, it enhances the steel production process.
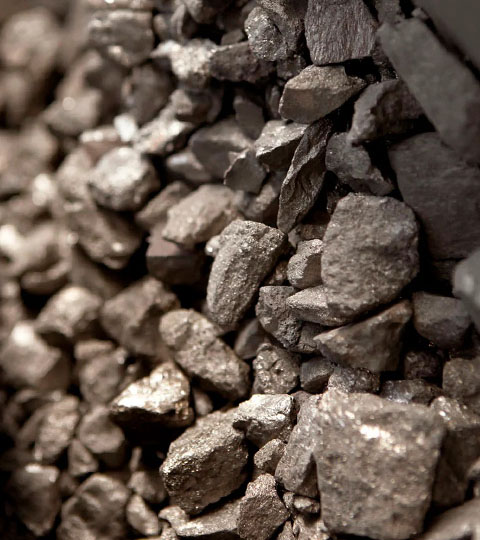
History of Direct Reduced Iron Use in Iran
The use of Direct Reduced Iron in Iran began in 2010 in induction furnaces. Although it was initially not widely accepted due to operational challenges, it has become one of the essential raw materials in the country’s steel industry with advancements in technology and the need to replace scrap iron.
Key Applications of Direct Reduced Iron
Steel Casting: Due to its high iron content, it plays a vital role in producing high-quality steel.
Induction and Electric Arc Furnaces: It is used as a substitute for scrap iron.
Iron Briquette Production: The fine Direct Reduced Iron is used to make iron briquettes.
Methods of Direct Reduced Iron Production
Direct Reduced Iron is produced through two major methods:
Gas-Based Method: Common in countries with natural gas reserves, such as Iran. Technologies like Midrex and HYL are used in this method.
Coal-Based Method: Used in countries with coal reserves, like India and China. Methods like SL/RN and Jindal are of this type.
Advantages of Direct Reduction over Blast Furnace
Reduced energy consumption and environmental costs
Possibility of small and medium-scale production
No need for expensive blast furnace equipment
Higher quality and greater purity of the produced iron
Conclusion
Direct Reduced Iron, as one of the most important raw materials in the steel industry, has a significant position in the steel supply chain by reducing production costs, increasing efficiency, and reducing environmental impacts. Iran, with its abundant natural gas resources, is a leading producer in this field, and the future of this industry in the country looks promising.
Metallurgical Coke
A Vital Component in Steel and Foundry Industries
Metallurgical coke is a porous carbon material with high strength that is produced by heating coal in the absence of oxygen. This process, known as carbonization, removes volatile substances from the coal and produces a high-carbon product. Due to its unique physical and chemical properties, metallurgical coke is one of the most critical raw materials in the production of iron, steel, and ferroalloys.
Coke Production Process
Metallurgical coke is produced by heating specific coals in coke ovens at high temperatures (about 1100 to 1300°C). During this controlled process, volatile substances are removed, leaving behind pure carbon. This process typically takes between 15 to 30 hours, and the final product is a hard, porous coke with high mechanical strength.
Wide Applications of Metallurgical Coke in Industry
Metallurgical coke is used in various industries due to its unique properties:
Steel Production: Its main use is in blast furnaces for iron ore reduction and steel production.
Foundry: Used as fuel and reducing agent in induction and cupola furnaces.
Ferroalloy Production: It serves as a carbonizing agent in producing ferromanganese, ferrosilicon, and other ferroalloys.
Chemical Industry: Used in the production of activated carbon, graphite, and other carbon products.
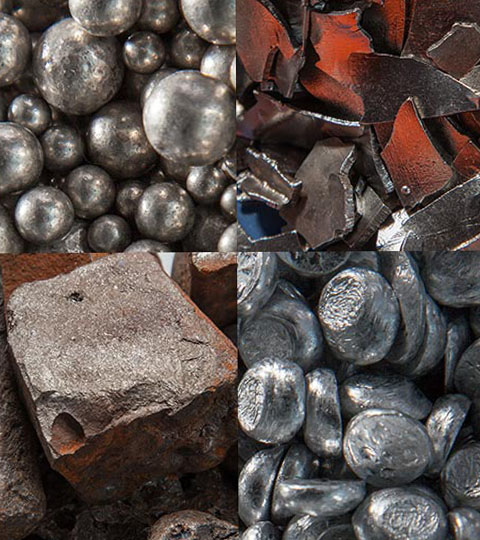
Importance of Metallurgical Coke in Steel and Alloy Production
Metallurgical coke plays a vital role in improving the physical and chemical properties of metals. Some of its benefits include:
- Increased strength and toughness of produced metals
- Reduced impurities such as sulfur and phosphorus
- Improved thermal efficiency and reduced energy consumption in metallurgical processes
- Ensured quality in producing alloy steels and high-resistance cast iron
Conclusion
Metallurgical coke is a key component in the metallurgy and steelmaking industries. With its unique properties, it enhances metal production processes. The quality of coke directly impacts the efficiency of furnaces and the final product’s quality. Therefore, controlling the production process and using appropriate raw materials is critical to producing high-quality metallurgical coke.